Understanding High Pressure Die Casting and Its Importance in Metal Fabrication
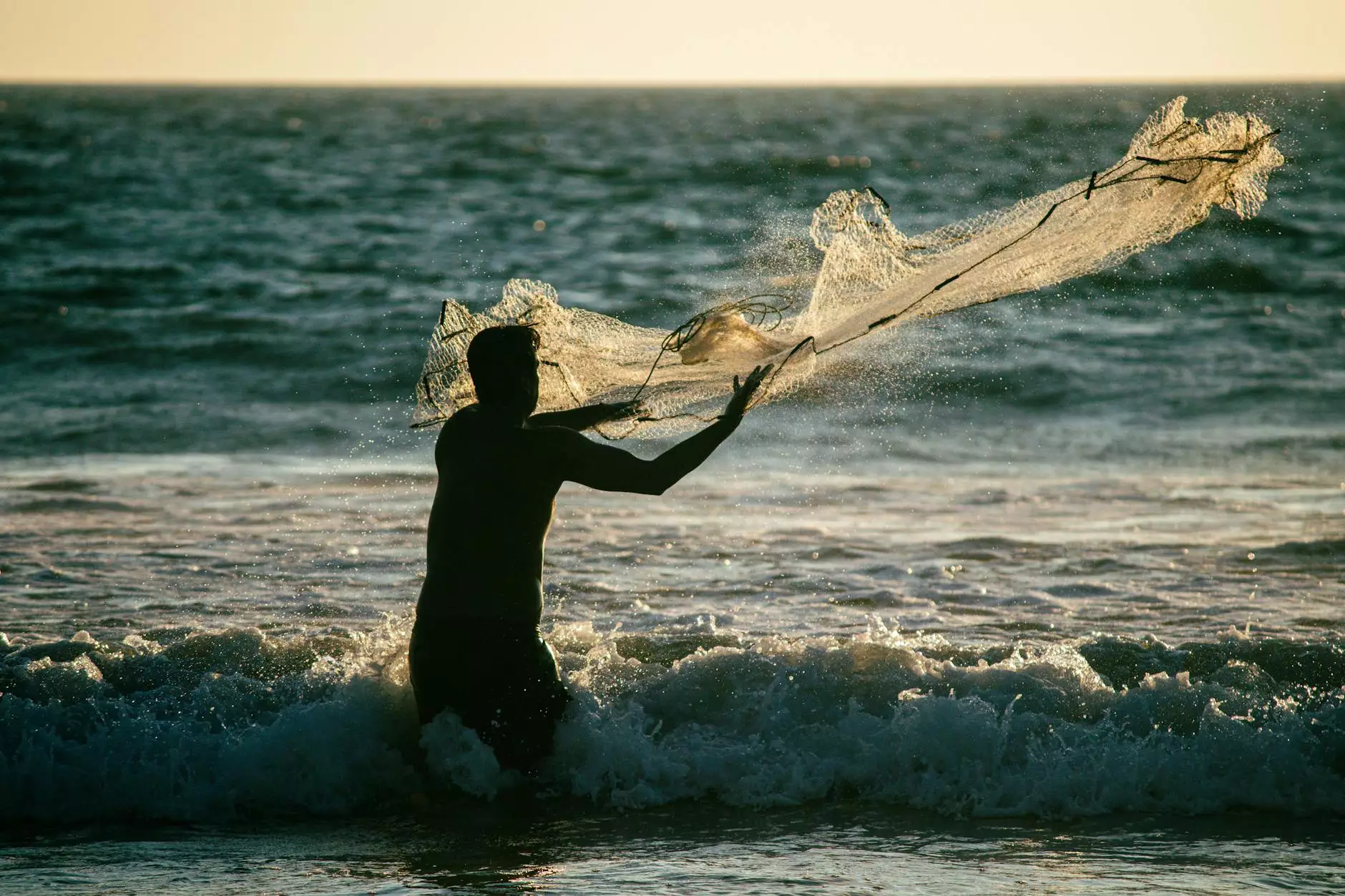
In the realm of metal fabrication, one of the most significant processes is high pressure die casting. This advanced manufacturing technique is pivotal for creating precise metal parts and components across diverse industries. At DeepMould, a leading high pressure die casting machine manufacturer, we delve deep into the intricacies of this technology, its applications, advantages, and the competitive edge it provides to businesses.
What is High Pressure Die Casting?
High pressure die casting is a manufacturing process that involves injecting molten metal into a mold at high pressure. This technique enables the production of complex shapes with excellent dimensional accuracy and surface finish. Commonly used metals for this process include aluminum, zinc, and magnesium, making it a versatile option in metal fabrication.
The Process of High Pressure Die Casting
The high pressure die casting process can be broken down into several key stages:
- Melt Preparation: The metal is heated until it reaches a molten state.
- Mold Application: A steel or aluminum mold, designed for the specific part, is secured in the die casting machine.
- Injection: The molten metal is injected into the mold under high pressure, typically between 1000 to 3000 psi.
- Cooling: The metal cools and solidifies within the mold.
- Ejection: After solidification, the mold opens to release the finished part.
Advantages of High Pressure Die Casting
Choosing high pressure die casting offers numerous advantages for manufacturers and industries alike:
- High Precision: The process allows for tight tolerances and complex designs.
- Surface Finish: Parts produced have a smooth surface finish, reducing the need for additional machining.
- Efficiency: The ability to produce large quantities of parts quickly makes it ideal for mass production.
- Material Efficiency: Minimal waste compared to other methods of manufacturing.
Applications of High Pressure Die Casting
The applications of high pressure die casting are vast and varied, with utilization across multiple industries including:
1. Automotive Industry
The automotive sector extensively employs die casting for manufacturing parts such as engine blocks, transmission cases, and chassis components, which require high strength and precision.
2. Aerospace Industry
In aerospace, high pressure die casting serves a critical role in producing lightweight, high-strength components that meet stringent safety standards.
3. Electronics Industry
The electronics industry benefits from die casting in the production of housings and frames for devices, ensuring durability and aesthetic appeal.
4. Consumer Goods
Manufacturers of consumer goods utilize this process for components found in appliances, furniture, and decorative items due to its cost-effectiveness and quality output.
Choosing the Right High Pressure Die Casting Machine Manufacturer
When selecting a high pressure die casting machine manufacturer, it’s essential to consider various factors:
1. Technology and Innovation
A reputable manufacturer should leverage the latest technology and innovation. At DeepMould, we pride ourselves on utilizing cutting-edge manufacturing techniques that enhance efficiency and quality.
2. Quality Assurance
High precision and quality products are a must. Ensure the manufacturer has rigorous quality control measures in place to meet industry standards.
3. Customization Options
Every business has unique needs. A good manufacturer should offer customization services to meet specific requirements.
4. Support and Service
Strong post-sale support and maintenance service are crucial for ongoing production efficiency.
DeepMould: A Leader in High Pressure Die Casting Machine Manufacturing
At DeepMould, we understand the dynamics of the industry and the critical role that high pressure die casting plays in modern manufacturing. Our commitment to excellence as a high pressure die casting machine manufacturer drives us to continuously improve our processes and technology.
Our Products
We offer a diverse range of high pressure die casting machines designed to cater to various industries:
- Aluminum Die Casting Machines: Optimized for producing lightweight and durable components.
- Zinc Die Casting Machines: Ideal for precise and complex geometries.
- Magnesium Die Casting Machines: Known for their strength-to-weight ratio, suitable for automotive and aerospace applications.
Innovation in Action
We pride ourselves on our continuous investment in research and development. Our team of skilled engineers works diligently to implement the best practices and innovations, enhancing the performance and reliability of our machines.
Future Trends in Die Casting
The future of high pressure die casting looks promising, with exciting trends shaping the industry:
1. Increased Automation
Automation is set to enhance efficiency and reduce labor costs in die casting processes. Smart manufacturing will drive faster production times with fewer defects.
2. Advanced Materials
New alloys and materials are being developed, expanding the capabilities of die casting technologies and applications.
3. Sustainable Practices
The industry is moving towards more sustainable practices, with a focus on reducing waste and energy consumption in the casting process.
Conclusion
In conclusion, being a reliable high pressure die casting machine manufacturer like DeepMould involves not only supplying machines but also contributing to the advancement of metal fabrication techniques. Embracing technology, ensuring quality, and focusing on customer needs are the cornerstones of success in this dynamic field. We remain committed to guiding industries toward their manufacturing goals, fostering innovation, and enabling superior quality production. Reach out to us today to learn how we can support your business in meeting its manufacturing needs.
For more information about our products and services, visit us at DeepMould.