Understanding Plastic Molding Factories: Innovations and Applications
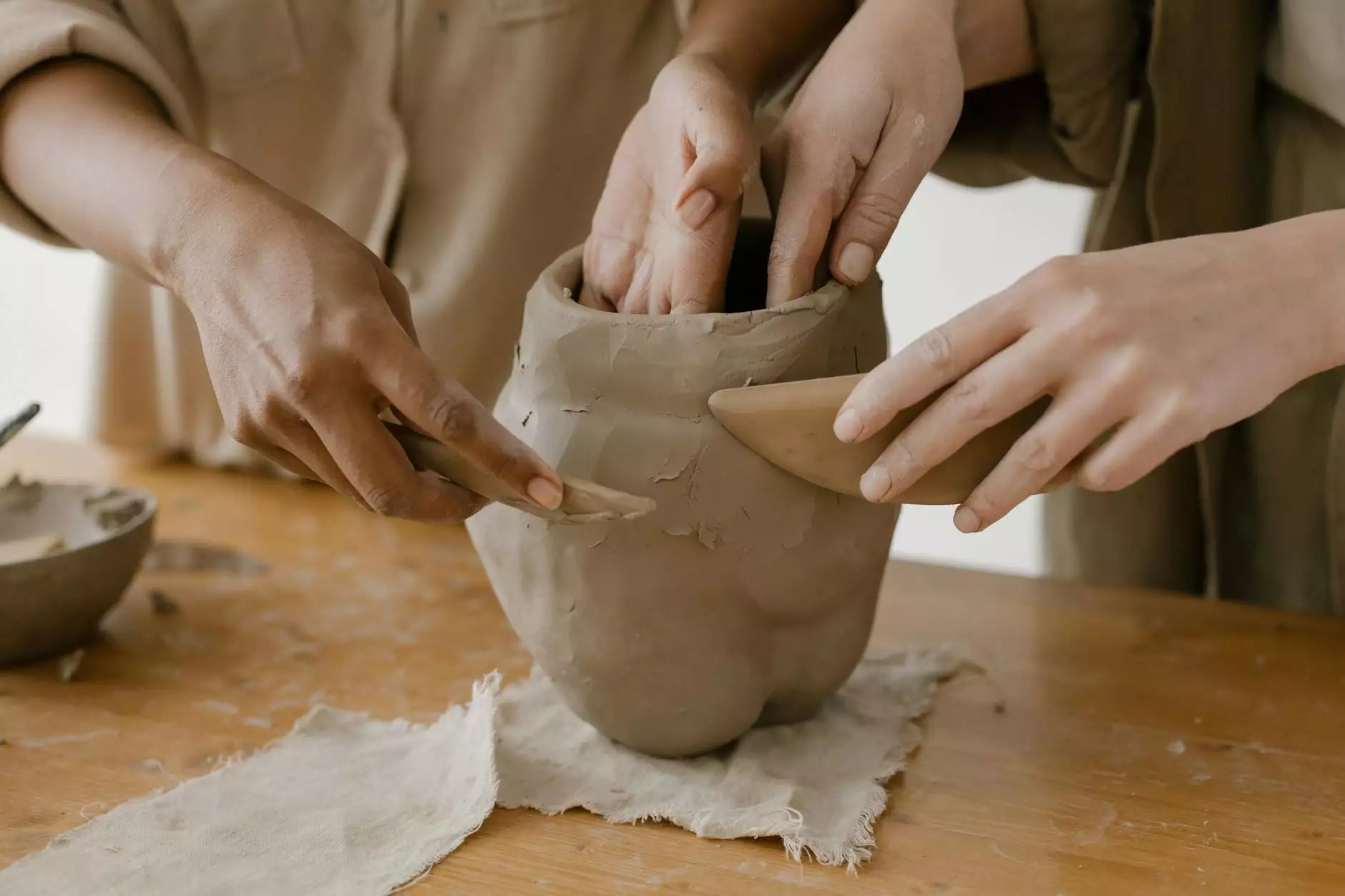
The Evolution of Plastic Molding
Plastic molding factories have significantly revolutionized manufacturing processes over the past few decades. Initially emerging as a response to the demand for efficient production techniques, these facilities harness advanced technology to create a myriad of plastic products.
The Role of Plastic in Modern Manufacturing
Plastics have become ubiquitous in contemporary society, playing vital roles across various sectors, including automotive, consumer goods, medical devices, and electronics. The durability, lightweight nature, and cost-effectiveness make plastics an ideal choice for manufacturers.
Key Processes in Plastic Molding
Understanding the processes involved in a plastic molding factory is crucial for grasping the intricacies of production. Here are the primary methods employed in the industry:
1. Injection Molding
Injection molding is one of the most popular methods due to its efficiency and versatility. The process involves:
- Material Preparation: Plastic resin pellets are heated until they melt.
- Injection: The molten plastic is injected into a mold.
- Cooling: The mold is cooled, allowing the plastic to solidify.
- Demolding: The finished product is removed from the mold.
2. Blow Molding
Blow molding is primarily used for producing hollow plastic parts, such as bottles and containers. This process involves:
- Extrusion: A tube of hot plastic is extruded.
- Blowing: Air is blown into the tube, expanding it to fit the mold.
- Cooling: The molded part is cooled and solidified.
- Trimming: Excess plastic is trimmed away.
3. Compression Molding
Compression molding is predominantly used for creating larger, heavier components. In this method:
- Material Loading: Plastic material is placed in an open mold.
- Heating: The mold is closed and heated, causing the plastic to flow and fill the mold.
- Curing: The material is allowed to cure before cooling.
- Finishing: The final product is removed and finished as necessary.
Advantages of Utilizing a Plastic Molding Factory
Engaging with a plastic molding factory presents businesses with numerous advantages, enhancing productivity and reducing costs. Some of these benefits include:
- High Efficiency: Automated systems in modern factories allow for high-speed production, significantly reducing lead times.
- Cost-Effective: Large-scale production diminishes per-unit costs, making it more affordable for companies to manufacture their products.
- Versatility: Factories can produce a wide variety of shapes and sizes tailored to specific product requirements.
- Minimal Waste: Advanced technologies have made it possible to recycle plastic materials, reducing waste and environmental impact.
Technological Innovations in Plastic Molding
As technology continues to advance, plastic molding factories are integrating innovative solutions that enhance production capabilities. Some noteworthy technological trends include:
1. Additive Manufacturing Integration
Many factories are incorporating 3D printing technologies to expedite the prototyping phase. This capability allows manufacturers to create precise models quickly and efficiently, paving the way for rapid product development.
2. Automation and Robotics
The inclusion of robotics in plastic molding factories has transformed manufacturing lines. Automated systems reduce human error, increase speed, and ensure consistent quality in production.
3. Advanced Material Science
Innovations in material science lead to the development of new plastic compounds that offer superior performance in terms of strength, durability, and resistance to weathering. Factories are increasingly utilizing these advanced materials to enhance their product offerings.
Quality Control in Plastic Molding Factories
Ensuring quality is paramount in a plastic molding factory. A robust quality control process involves:
- Material Inspection: Raw materials must be inspected for quality before production begins.
- Mold Checks: Molds are frequently inspected and maintained to avoid defects.
- Process Monitoring: Live monitoring of production processes ensures that any deviations from standards are addressed promptly.
- Final Product Testing: Finished products undergo rigorous testing to ensure they meet all specified requirements.
Environmental Considerations in Plastic Molding
As environmental concerns rise, plastic molding factories are adopting sustainable practices. Initiatives include:
- Recycling Programs: Implementing systems to recycle waste plastic helps minimize environmental impact.
- Energy Efficiency: Upgrading machinery to more energy-efficient models reduces overall energy consumption.
- Biodegradable Plastics: Research and development into biodegradable alternatives helps pave the way toward more sustainable manufacturing practices.
Case Studies: Successful Plastic Molding Innovations
Various companies have excelled in implementing innovative practices within their plastic molding factories. Here are a few key examples:
Case Study 1: A Leading Beverage Manufacturer
A major beverage company leveraged blow molding technology to produce lightweight bottles. By altering the design and material composition, they achieved a reduction in plastic usage by 20%, significantly lowering production costs while enhancing sustainability.
Case Study 2: Automotive Components Producer
An automotive parts manufacturer utilized advanced robotics in their injection molding processes, dramatically increasing throughput. This transition not only reduced labor costs but also improved overall product quality, resulting in higher customer satisfaction ratings.
Future Trends in Plastic Molding Factories
The future of plastic molding factories promises exciting advancements, including:
1. Increased Customization
With the rise of consumer demands for personalized products, factories are expected to adopt technologies that allow for greater customization in production runs.
2. Enhanced Supply Chain Integration
Digital transformation will enable factories to integrate their operations more closely with suppliers and distributors, improving efficiency and response times.
3. Eco-Friendly Practices
The industry is likely to see a continued shift toward sustainable practices, including the use of alternative materials and closed-loop recycling systems.
Conclusion
In conclusion, the role of plastic molding factories in modern manufacturing is indispensable. They not only facilitate the efficient production of a wide array of plastic products but also continue to innovate to meet the changing demands of various industries. By leveraging advanced technology, emphasizing quality control, and adopting sustainable practices, these factories are poised to lead the way in the future of manufacturing.
Call to Action
If you're looking to partner with a reputable plastic molding factory, explore the solutions offered by Deep Mould. Our commitment to quality, innovation, and sustainability makes us a leader in the metal fabrication and plastic molding industry.